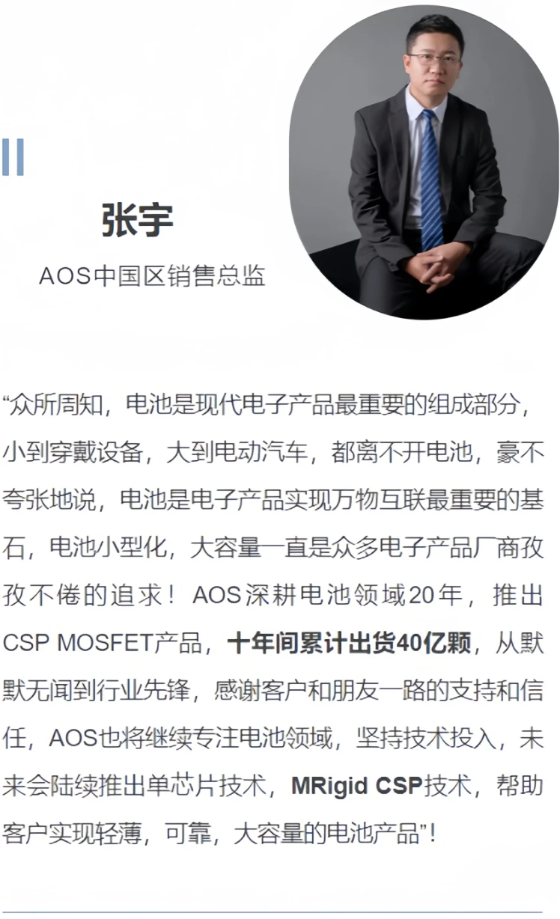
在6月5日,充电头网举办了关于快充时代的AOS电池保护解决方案研讨会的线上直播。本次直播由AOS资深市场经理何黎与AOS应用工程经理张军共同主讲。他们围绕AOS电池保护解决方案展开深入研讨,分享最新的研究成果和实践经验。
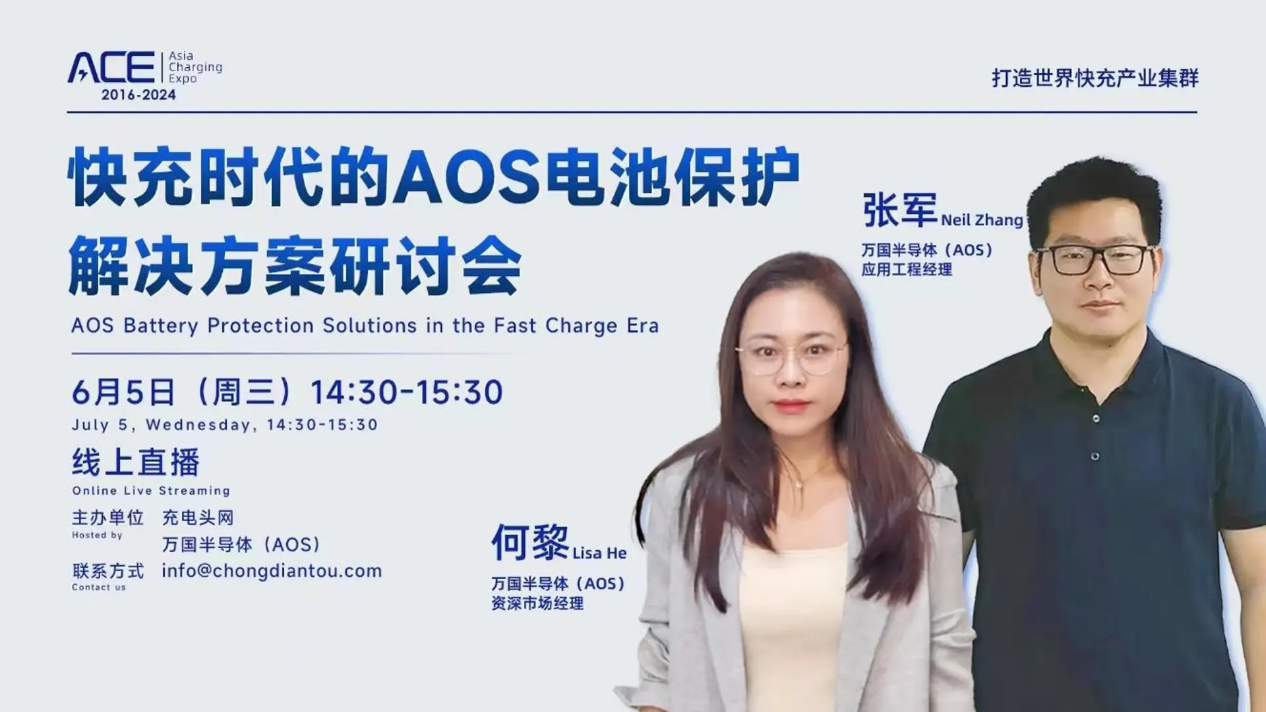
现在,让我们一起来回顾一下这次直播的精彩内容。
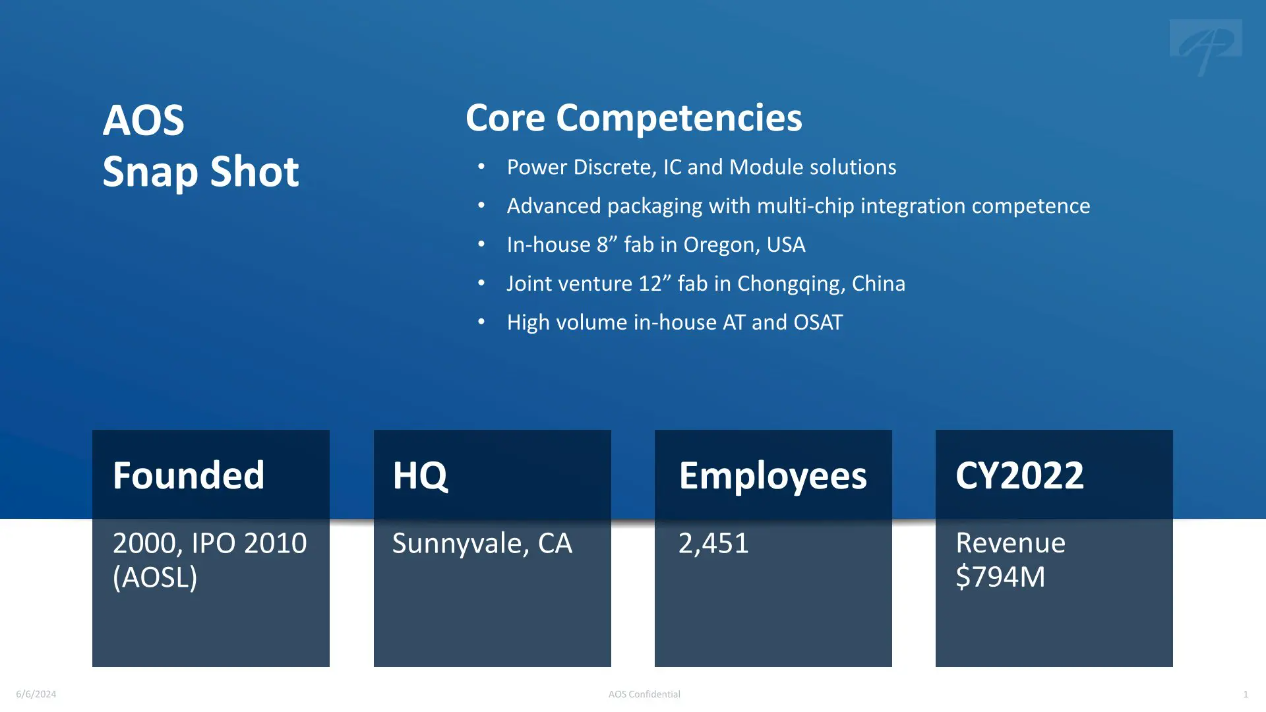
AOS公司成立于2000年,并于2010年在纳斯达克上市。公司总部位于美国加利福尼亚州硅谷的桑尼维尔市。目前,AOS在全球范围内雇佣了大约2500名员工。在2022年时,公司总收入约为8亿美元。
AOS作为一家成立超过20年的IDM半导体供应商,拥有完整的生产和封测设施。公司总部位于美国硅谷,在俄勒冈州设有八寸晶圆厂,在重庆有十二寸晶圆厂和封测厂,在上海松江设有全资封测厂,专注于先进封装和研发。此外,公司在泰国和马来西亚也设有封测厂,以满足全球供应链的需求。AOS的产品涵盖了包括Power IC,碳化硅MOSFET,IGBT、HV Super Junction以及中低压MOSFET在内的多条产品线,致力于为客户提供完整的电源解决方案。2022年,AOS在全球功率器件市场排名第六。
从2012年到2024年,AOS的CSP产品累计出货量已经超过40亿颗,能够取得这样的成绩,离不开客户的信任和支持。在便携式设备电池保护领域,AOS的市场份额处于行业前列,也将在未来持续为客户提供高质量的解决方案。
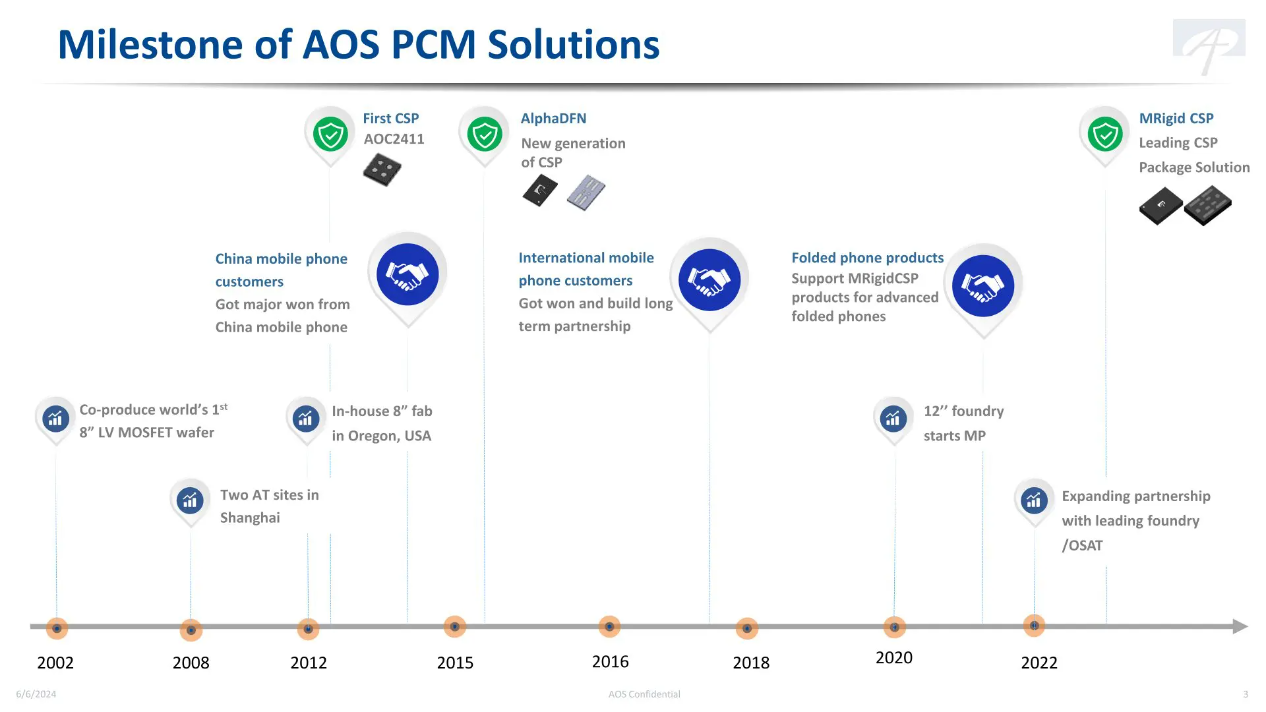
AOS自2012年开始生产第一颗CSP,到2014年已与国内主要手机客户建立合作。到2017年,AOS又与两家国际主要手机品牌达成合作。从2020年到2021年,AOS推出了适用于折叠手机和小型化手机的电池保护产品,并持续进行技术更新。
CSP市场的需求非常巨大,特别是在智能手机领域。2024年,全球智能手机的出货量预计在11亿到12亿之间。因此,用于手机电池保护的MOS管需求量极其庞大。除了技术和封装的不断进步,产能的提升也是关键,必须能够满足主要客户的需求。
在产能方面,AOS从2012年主要依靠美国的八寸晶圆厂,到2018年在重庆的12寸晶圆厂开始生产CSP相关产品。2020年,AOS首款12寸晶圆制造的CSP产品量产并获得客户认证。AOS是最早使用12寸晶圆制造CSP产品的公司之一, 自2020年起AOS就开始与国内的晶圆和封测厂商合作,进一步拓展产能和满足客户多样化供应链的需求。
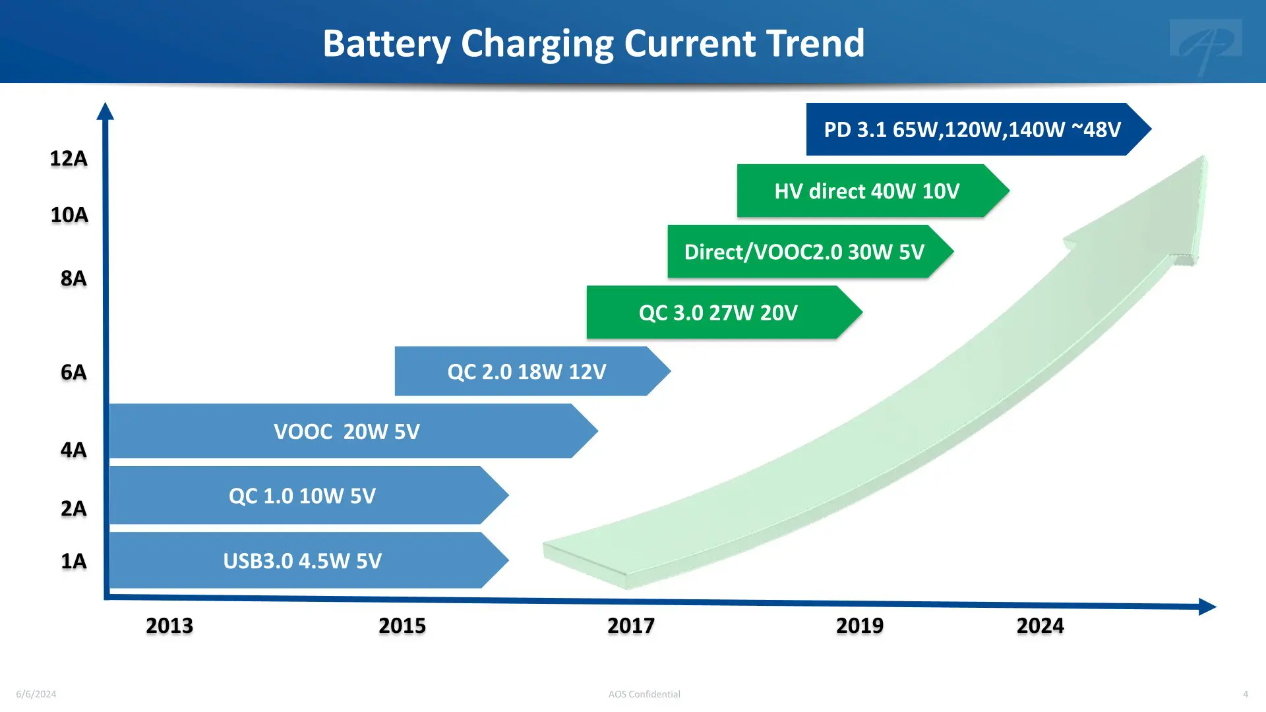
在过去几年中,手机电池的性能一直在不断提升,包括充电速度的增加和电池容量的扩大,用户对续航时间的需求也在不断增加。
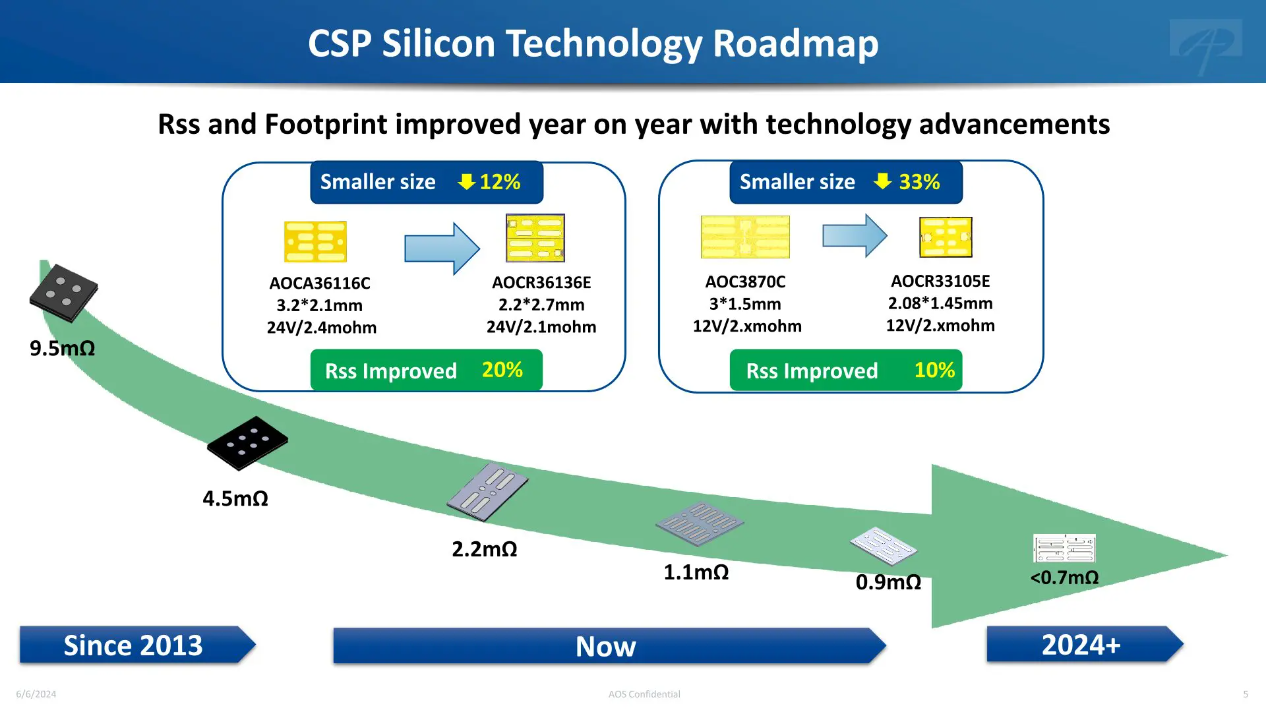
为了应对这些挑战,MOS管需要在体积和导通内阻上不断进行优化,以减小损耗并提高效率。通过不断降低导通电阻和缩小体积,MOS管在手机电池中所占的功耗比例也在减小,从而延长了续航时间。同时,通过减小体积,手机内部有更多空间容纳更大容量的电芯,进一步增加了续航时间。
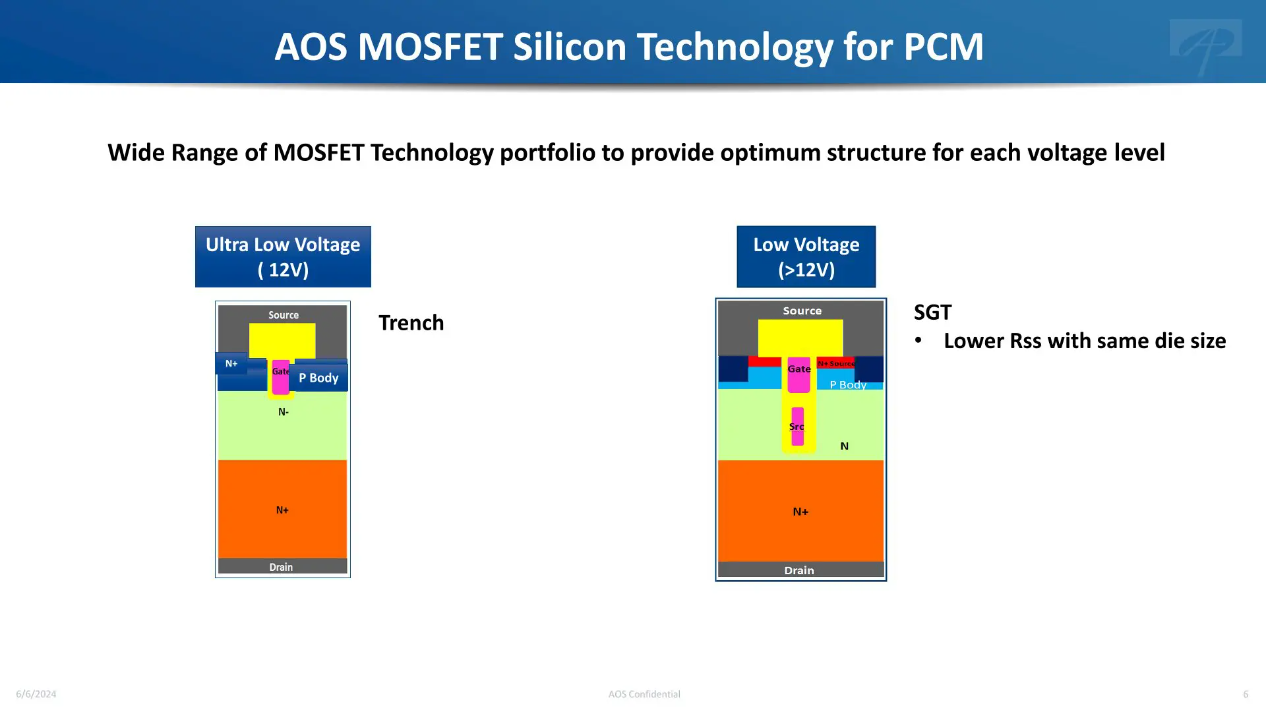
AOS针对不同电池应用采用不同晶圆技术,以提高性能和降低内阻。针对12V以下应用,AOS采用传统trench结构,并通过改进原材料提升内阻;而对于12V以上的应用,采用SGT结构,能更有效提升导通内阻。SGT技术在大于20V的应用中,相比传统结构具有更小的晶圆面积,以实现相同的导通电阻。
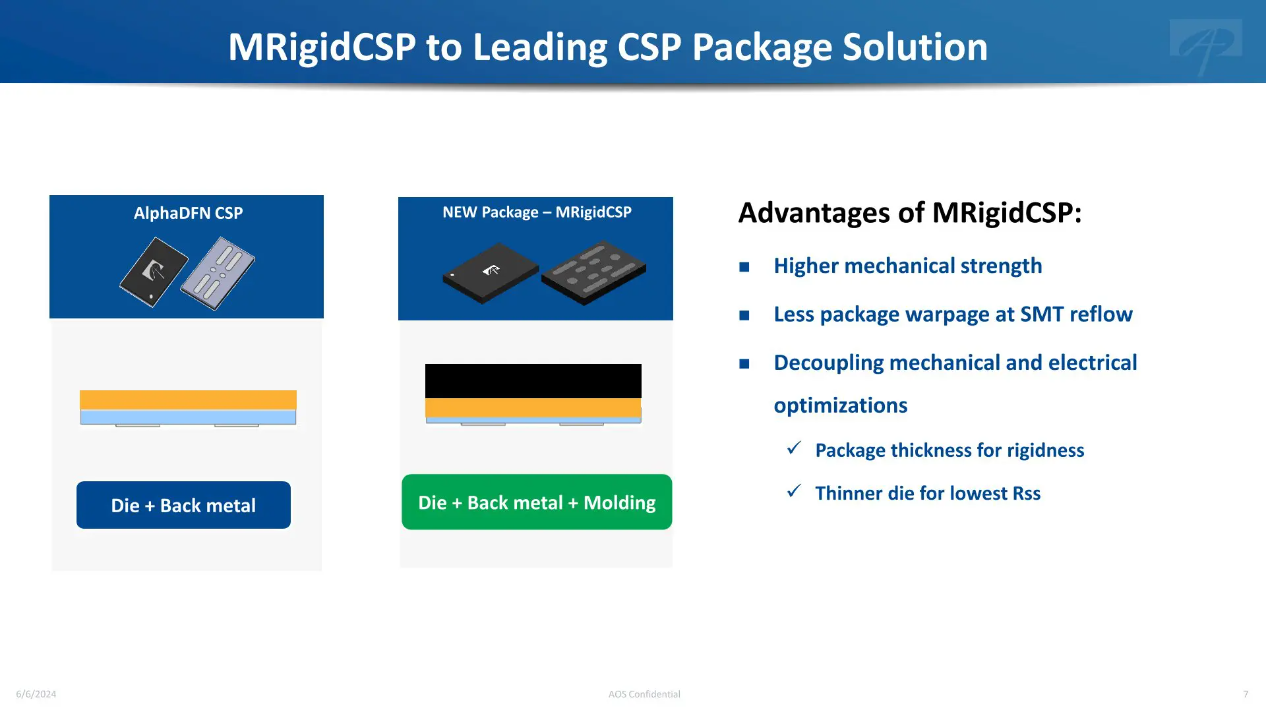
除了晶圆制造外,后端封测也至关重要。厂商在追求高性能的同时,也要应对机械应力问题,这对CSP产品是个挑战。传统方法是通过减少晶圆的厚度来降低RSS,但这会减弱器件承受机械应力的能力。AOS推出了MRigidCSP解决方案,将性能和机械应力分开实现,通过特殊工艺在晶圆上实现薄化,而将机械应力转移到另一层molding上,以实现低RSS和更好的机械性能。这种技术的实现需要花费数年时间,但AOS已经成功实现量产,并推出了不同Vds和Rss等级的产品。
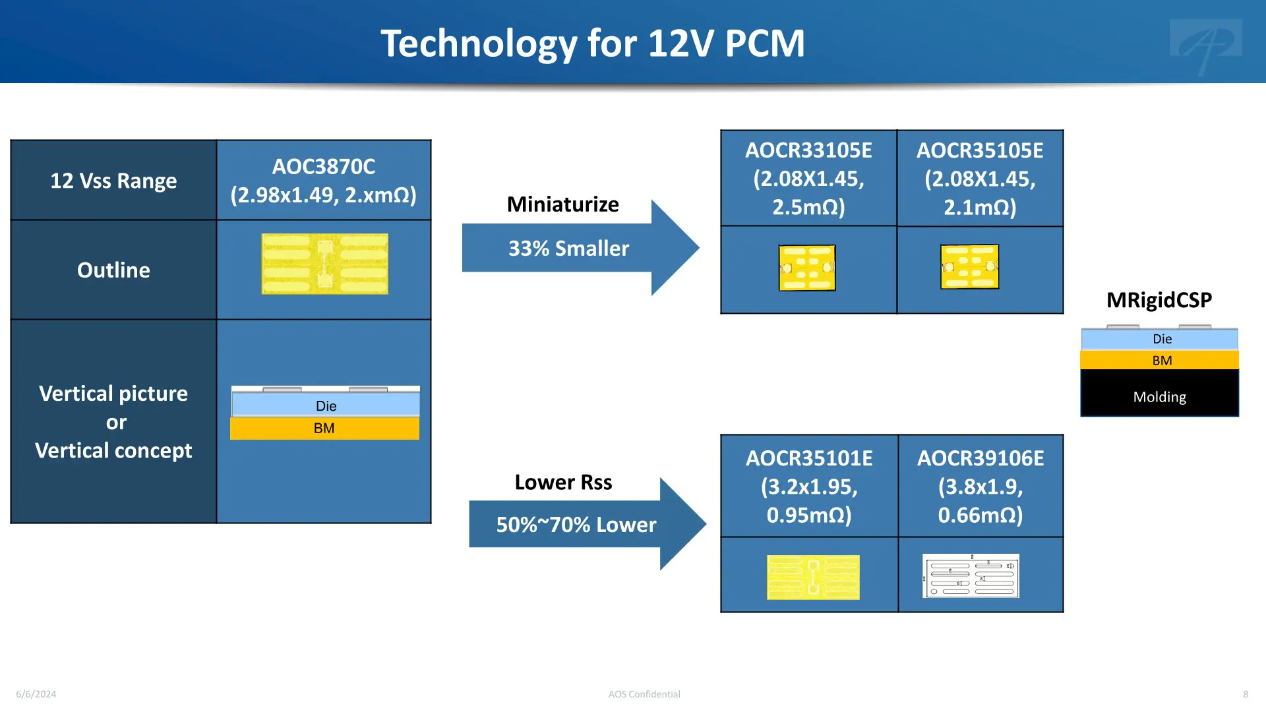
目前市场上主流的产品趋势是小型化,AOS产品尺寸可减少约33%,但性能保持不变,使得CSP在应用中所占的面积越来越小。另一种方式是在保持体积差不多的情况下进一步降低RSS。AOS最新一代产品采用MRigid技术,实现的RSS可达0.95mΩ,甚至可以进一步降至0.66mΩ。
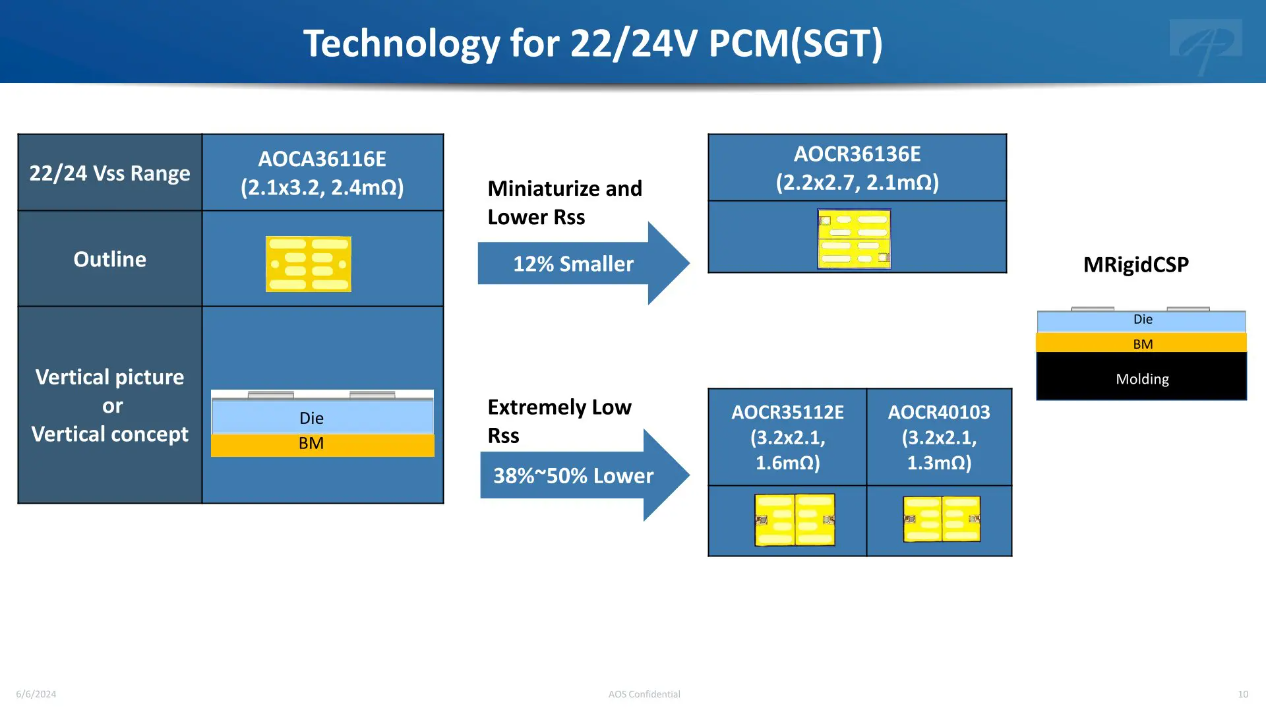
同样对于>20V的产品,AOS将SGT的晶圆技术和Mrigid的封装技术相结合,实现了在体积和Rss的进一步减小,导通损耗降低多达50%,为客户实现更大电流密度的设计。
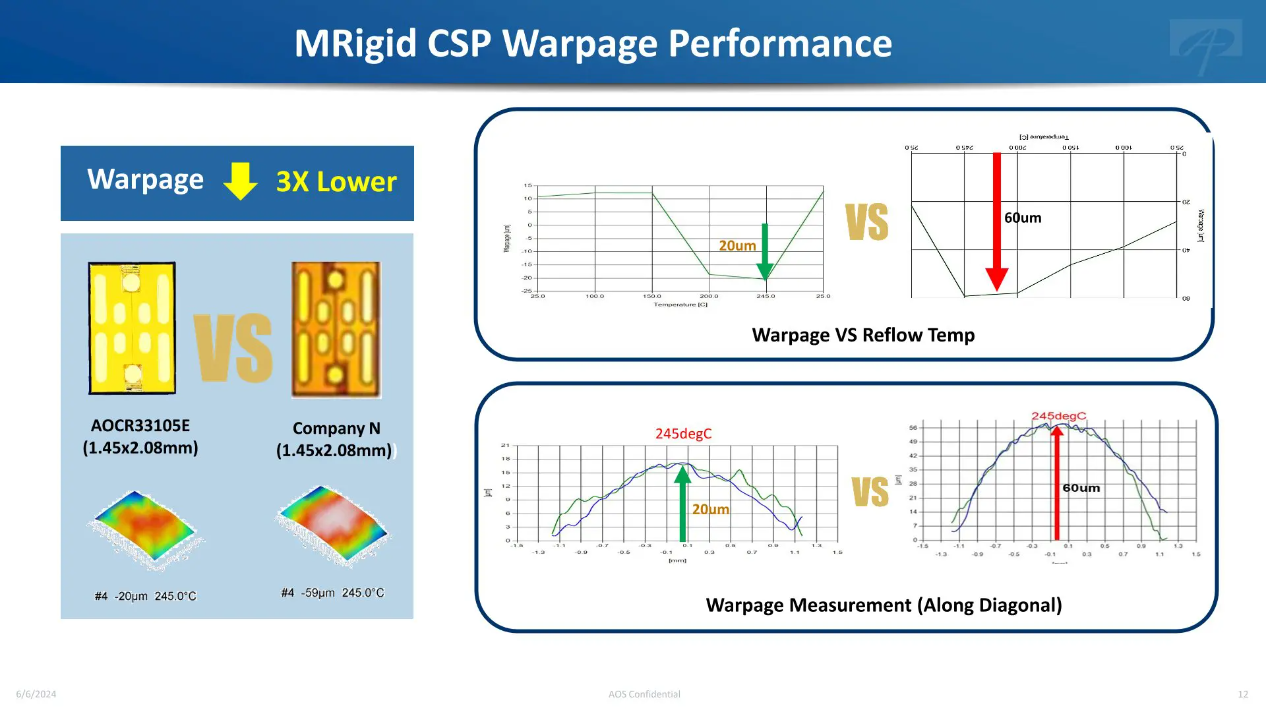
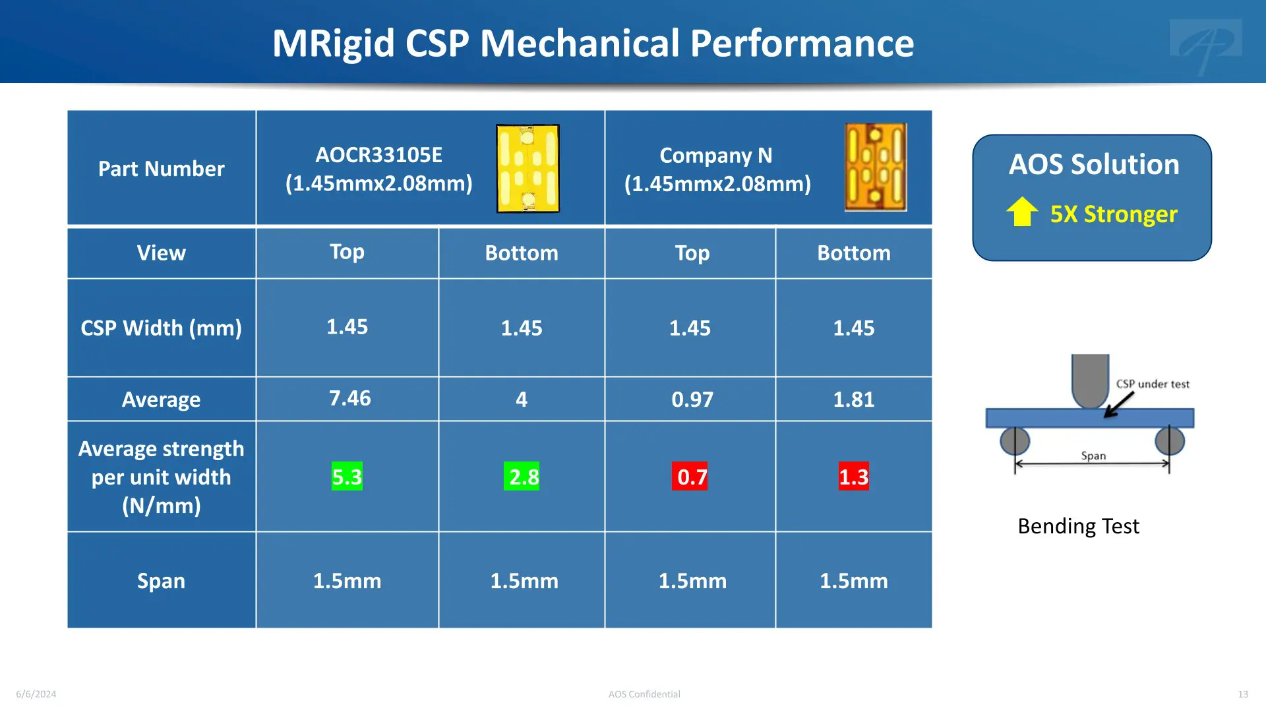
除了电性能外,CSP还有两个重要的性能,即高温下的翘曲和机械强度。
翘曲是指在过回流焊时,高温引起的形变,器件越薄,形变的尺度越大,越会造成焊接或者形变失效,AOS MrigidCSP完美的解决了这类问题,在回流焊高温下形变不超过20um,小于竞争对手三倍。
其次是机械应力,即CSP能够承受的压力和应力情况。相比市面上主流竞争对手的CSP,AOS的产品由于采用了molding层材料,其机械强度可以达到他们的5倍以上,这使得AOS的产品更加强壮,在客户生产和运输中都具有更高的可靠性。
除了便携式设备以外,AOS也在跟终端客户不断合作和探讨把CSP产品应用到更多的锂电池设备,希望其体积小性能优的优势可以助力其他有锂电池保护的的终端产品实现更长的续航和更小的体积,高性能PC是目前探讨的一个方向,传统封装器件因具有较低的成本和较高的可靠性,通常适用于空间较大的笔记本内部。然而,随着AI技术的普及,笔记本的计算能力和功耗显著增加,部分型号的功率已达400W,对电池续航提出了更高要求。AOS正在与PC厂商合作,尝试通过CSP方案解决空间占用小、温度低、电池保护效率高的需求,这成为CSP技术的新应用方向。
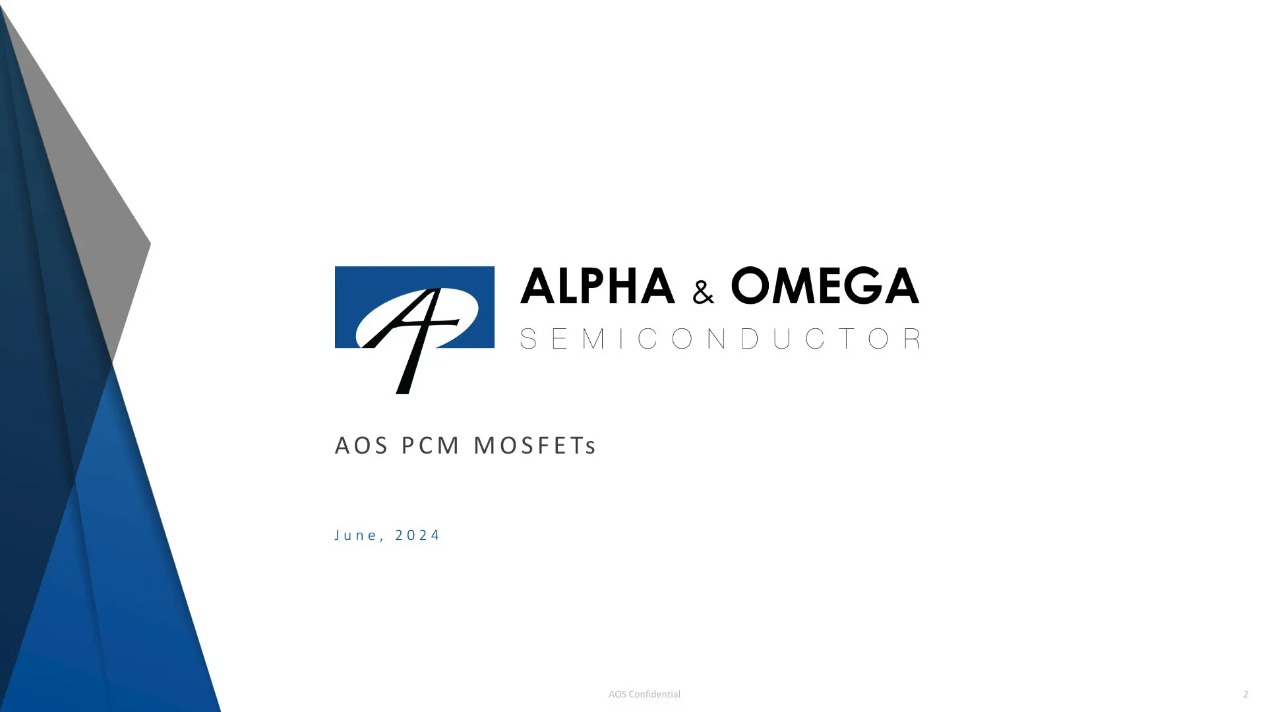
锂电池是移动设备能量的重要来源之一,具有体积小巧,功率密度高等优势。随着锂电池技术的发展,其功率密度在不断提升,相同体积下可以延长设备的使用时间,但也带来充电时间延长的问题。为了解决这一问题,快充技术逐渐成为主流。同时为了确保快充过程的安全,电池模组中通常配置保护电路板(PCM)。
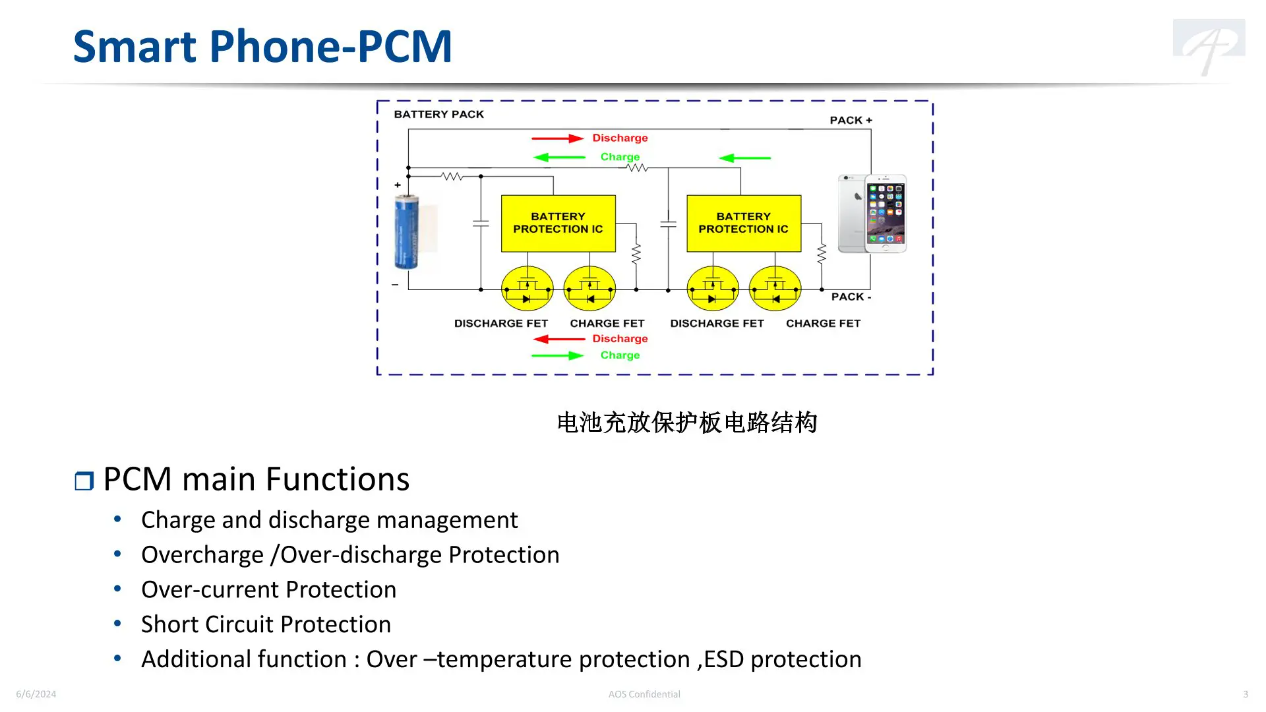
PCM包括一个实时监测电池状态的专用IC和一个能够检测异常并快速关断的开关。该开关串联在电池、充电器或负载之间,充电和放电都通过它进行,因此需要考虑开关的损耗。为了高效充放电,必须将开关的损耗降至最低。MOSFET因具有低导通电阻,成为最通用的功率器件,用作开关,可以实现更高的充放电效率。同时PCM还可进行过充、过放、过流、短路、过温等一些方面的保护。
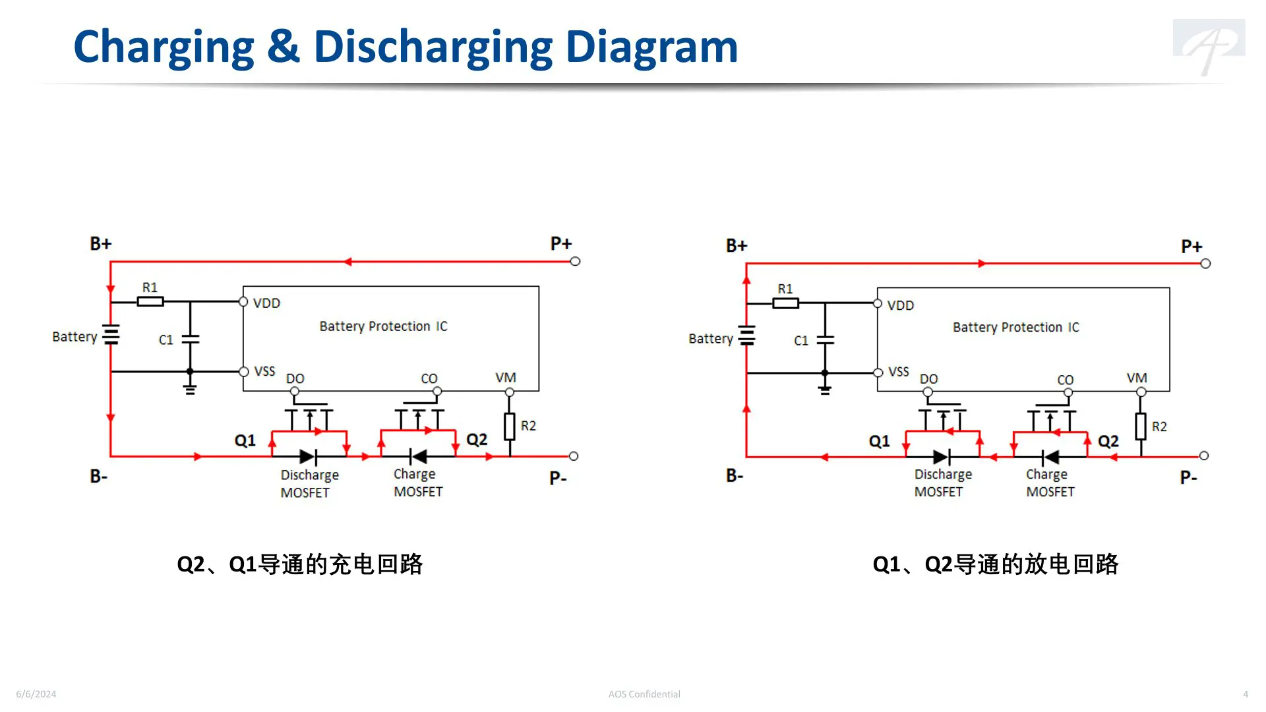
PCM模块在充电和放电过程中往往能起到关键作用。在充电时,会打开Q2充电管,使电流从充电器正极流向电池,再流向负极,形成充电回路。为降低导通损耗,背靠背的MOSFET Q1也会同时打开,实现高效充电。如果充电电压超过4.28V,会导致电池失效或过热,甚至爆炸。此时,IC会实时监测电压,当检测到过压、过流或过温时,迅速关断MOSFET,切断充电回路。放电时,电池给负载(如手机)供电,打开放电MOSFET Q1实现放电回路,同时背靠背的充电MOSFET Q2也会打开,降低导通损耗,提高放电效率,延长电池使用时间。如果电池深度放电(一般低于2.7V),IC检测到过放、过流或过温情况时,会关断放电MOSFET,切断放电回路,从而保护电池。
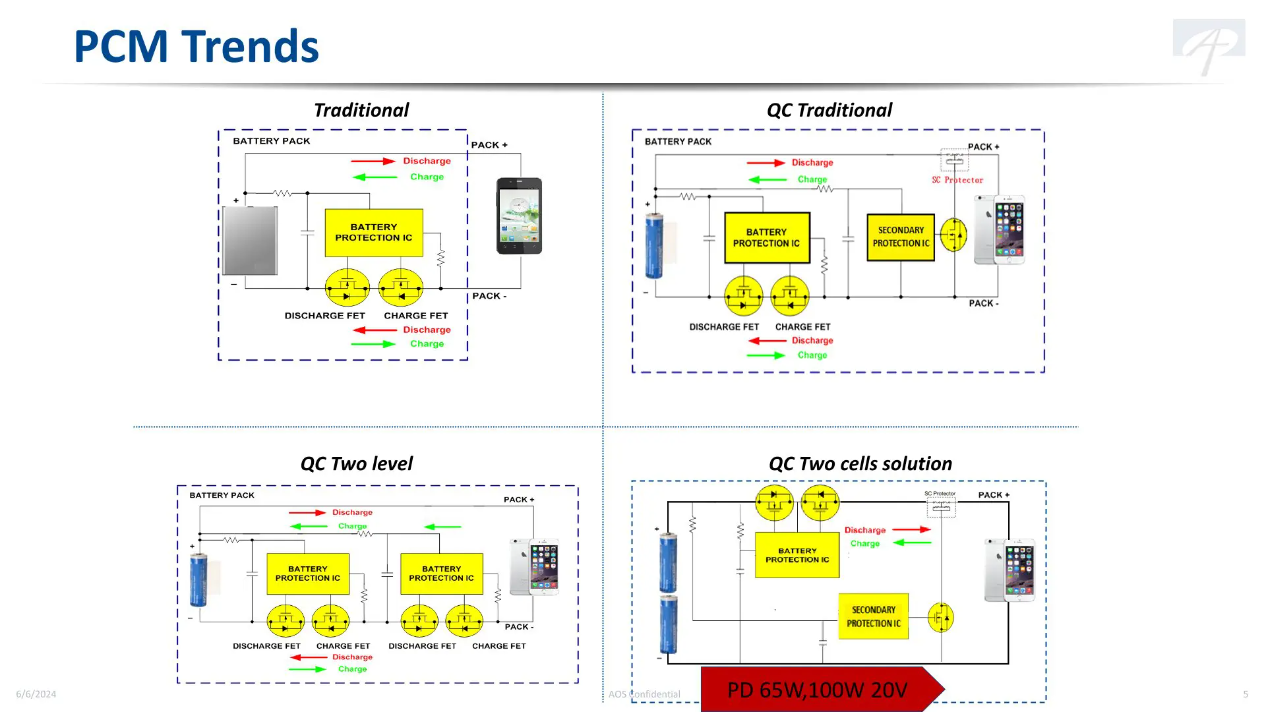
PCM模块有多种配置方式,常见的一种是将两个背靠背的MOSFET放置在电池的负极端,这种配置驱动简单,但为了满足安全标准,需设置两级保护,以防止MOSFET失效短路导致过压直接作用于电池。另一种方案是在电池正极端放置MOSFET,这种高端配置的驱动需要更强的IC支持,安全性更高,因为如果IC失效,驱动信号丢失时MOSFET会自动关闭,隔离电池与充电器或负载。除了两组背靠背MOSFET的二级保护外,还可以通过电阻保险丝实现二级防护。
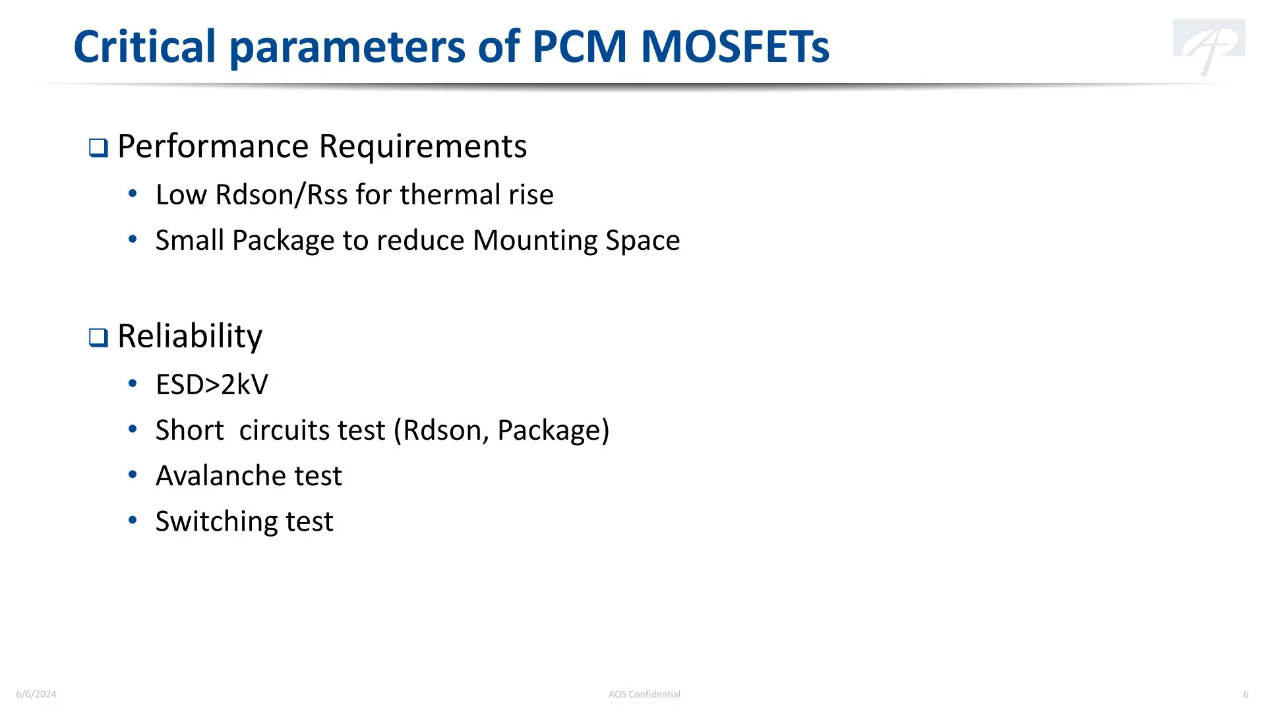
应用在手机端的电池PCM模块有几个主要需求。首先,随着手机电池容量的不断增大,从早期的600毫安时、1000毫安时到现在的3000毫安时、6000毫安时甚至更多,为了实现快速充电,需要增加充电电流,这对MOSFET的导通电阻提出了更高要求。导通电阻不够低会导致自身损耗和发热,增加风险。
其次,PCM模块通常安装在电池包的侧面,宽度非常窄,约为三到四mm。在有限的空间内,需要放置两个MOSFET及其他电路元件,因此必须采用最小最薄的器件。此外,PCM模块还需具备高可靠性,要求ESD抗静电能力大于2KV,并能承受短路大电流。布局不良可能引发雪崩效应,器件也需具备抗雪崩能力,且开关性能必须优异。
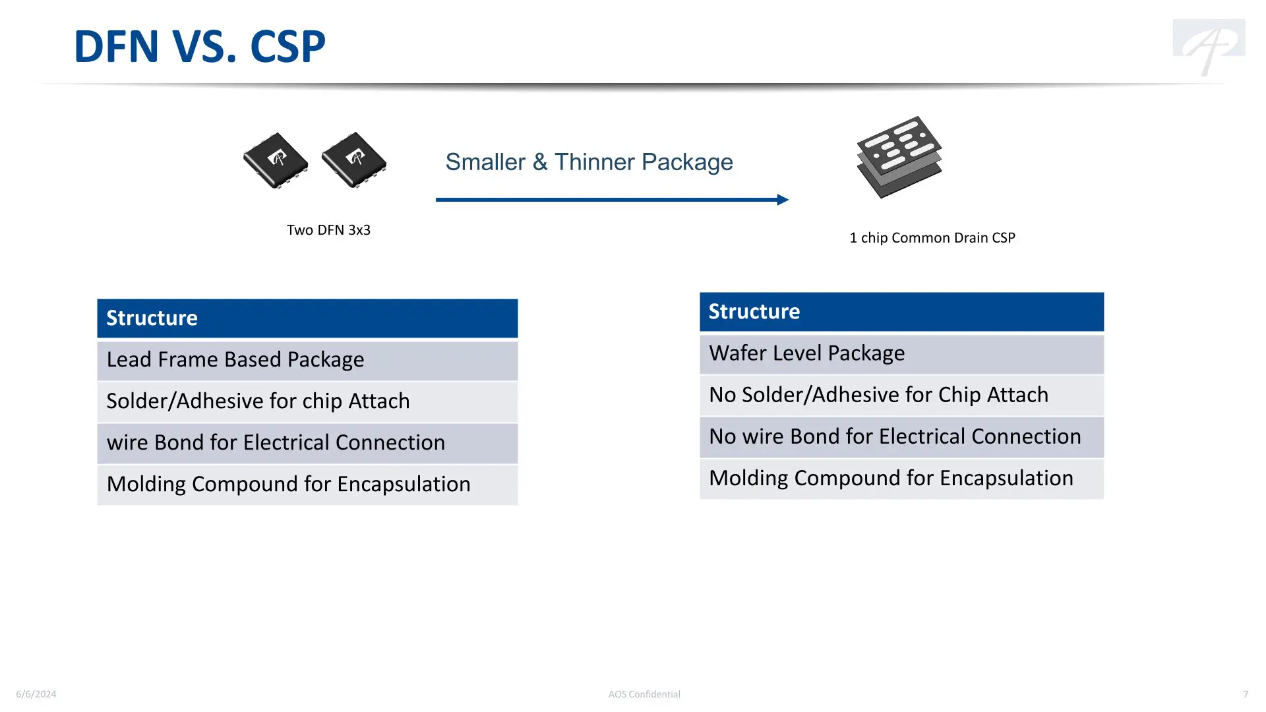
针对上述要求,AOS从两个方向进行优化,分别是晶圆和封装。首先,在晶圆方面优化了工艺,开发了专为PCM应用设计的CSP(Common Drain CSP)。这种CSP在一个衬底上共有两个MOSFET,通过中间的隔离实现分离。这样设计使得同样尺寸的芯片面积更大,导通电阻更低。同时,通过优化结构,在保持耐压的情况下尽量减薄硅片,进一步降低导通电阻。
其次,在封装方面,采用芯片级直封技术,将芯片直接焊接在PCB板上,消除了外封装连线的电阻影响,也不再需要PAD与芯片之间的连接材料,降低了热阻,显著提升了散热性能。
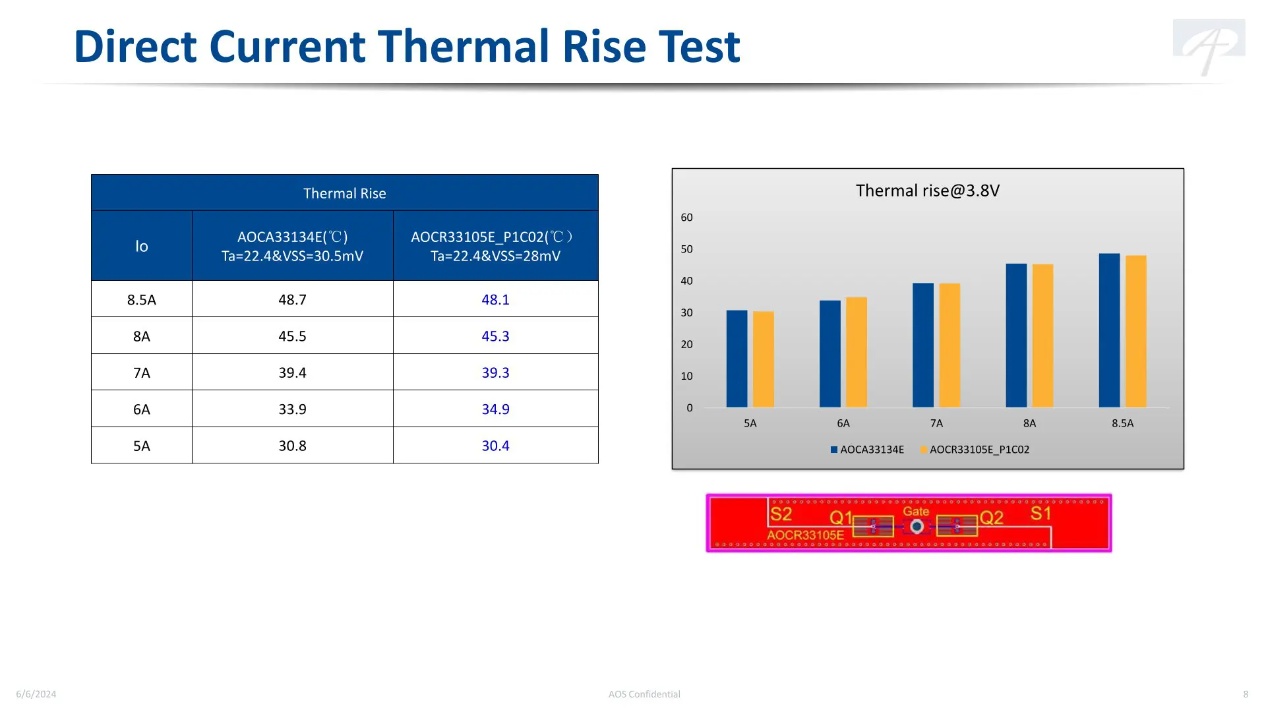
对于手机快充应用,尤其是PCM,温度控制至关重要,因为高温会对电池造成影响。一般而言,手机快充应用中,根据行业标准,常温条件下,PCM的温度在满载情况下不应超过65摄氏度。在上图测试中,得到的温度在50摄氏度以下,表现非常优异。
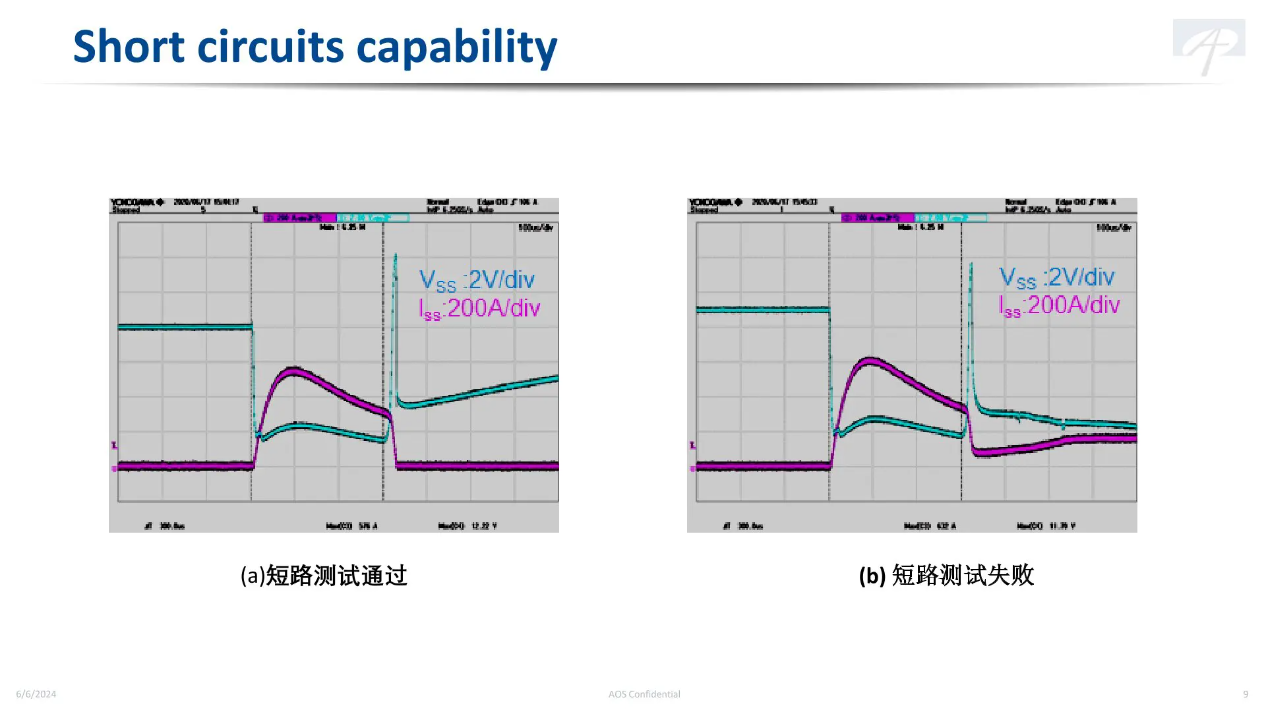
除此之外,AOS还会针对每个产品做短路测试验证。因为在极端情况下,负载短路可能会导致电池释放出大电流,而芯片会监测到这个电流,并会延迟一段时间后关闭,这段时间大约是280微秒。在这段时间内,产品必须能够承受住这个大电流的冲击,否则可能会带来严重后果。AOS针对每个产品都验证了其短路电流能力,测试结果显示,产品的电流能力大约达到了500A,远远超过实际线路中电池产生的电流,这表明产品有很大的安全余量。
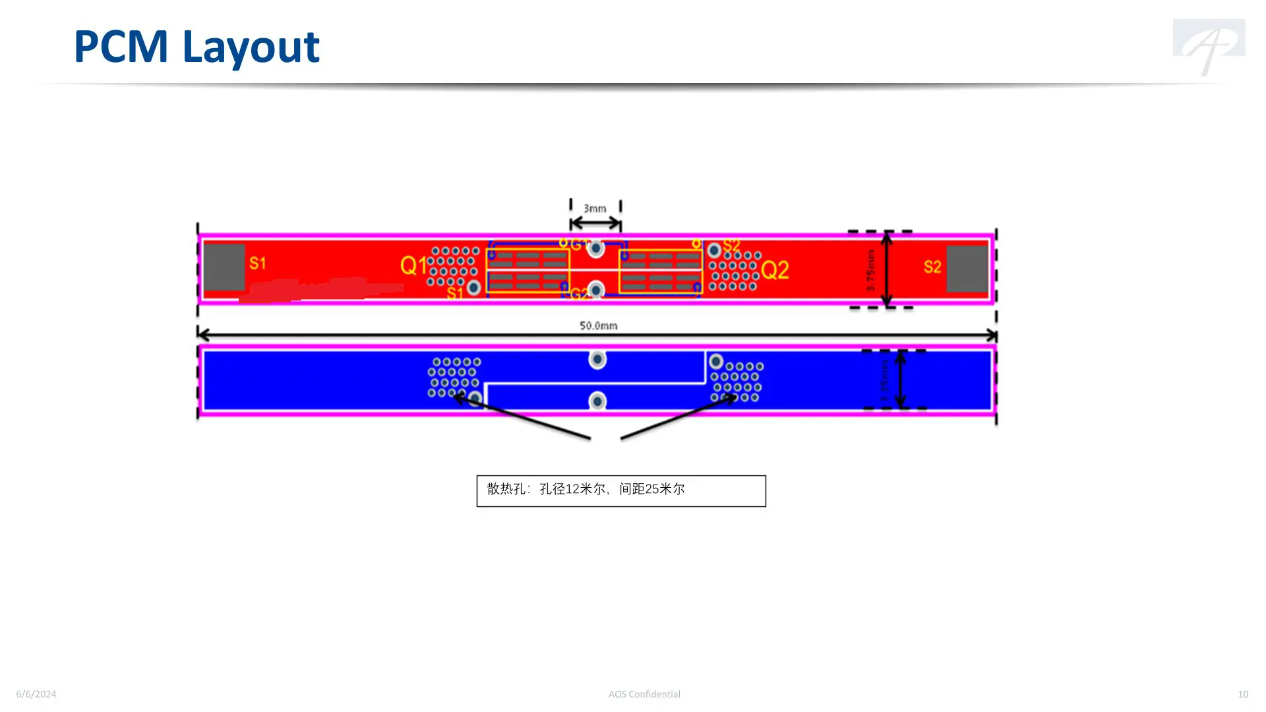
另外一个重要方面是关于PCM产品的PCB布局设计。以一个47W的快充为例,其充电电压为5V,电流达到9.4A,因此可能需要两颗CSP产品并联。我们使用AOS的导通电阻约为0.8mΩ的产品。电流路径采用上下对称,保持电流均衡。两颗MOS之间间隔3mm,避免相互加热。尽可能的增加功率路径铺铜面积,并且在靠近MOSFET的铜皮上增加散热孔以增加散热,减小MOSFET温升。除此之外,还需要验证其雪崩能力和ESD能力。
充电头网总结
AOS作为一家成立超过20年的半导体供应商,在生产制造和技术研发方面有着丰富的经验和领先的水平。从早期的晶圆制造到后端封测,AOS始终保持着对技术的不断创新和提升,结合了先进的电池管理技术和智能算法,旨在为客户提供高质量的解决方案。
MRigidCSP具有非常优异的导电性能和机械性能。通过采用先进的封装工艺和材料,该技术成功实现了导通电阻的大幅降低,从而提高了电池的充电速度和效率。同时,该技术还增强了封装体的机械强度,使其能够承受更高的压力和振动,保证了电池在复杂环境中的稳定性和安全性。同时,AOS还积极探索新的应用领域,如PC端电池保护,为整个行业带来了更多可能性。
相信在未来,随着移动设备技术的不断发展和市场需求的不断变化,AOS将继续致力于创新,不断提升产品性能和用户体验,为客户提供更加全面、可靠的解决方案,助力移动设备行业迈向更美好的未来。
相关阅读:
评论 (0)